More than 100 years committed to technical progress has made us the leading manufacturer in the fields of variable AC drives, servo drives, control technology and robotics.
Robotics Software
MotoLogix
Programming Robots via PLC Function Blocks
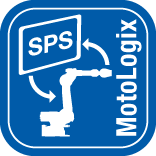
Overview
MotoLogix is a software interface for teaching and programming MOTOMAN robots using PLC function blocks.
No Teach Pendant or Yaskawa-specific robotics knowledge is required to program, test or operate the robot. All code remains in the PLC environement together with the line PLC programs, even all backups. In the background, the robot control hardware (without the TeachPendant) is still there, but just for motion planning and keeping the Servo and Power supply hardware in one cabinet. This is why the motion quality and speed performance keeps untouched in case of PLC-based programming.
What is the Benefit of PLC-based Robot programming?
Many companies are well staffed with PLC programmers, but complain about shortage of robot programmers.
If you need to integrate robots into your PLC controlled automation line only here and there, you may not want to build up extra capacity and robotics know-how for doing so - it would raise your headcount in terms of robot programming, commissioning and service, along with additional efforts th keep them trained and experienced. Subcontracting robot programming services may not be available or too expensive, when your robotics know-how which you learned along the way has been lost again due to lack of practice.
OEMs (machine tool or packaging machine manufacturers) also prefer to integrate and program robotic automation their within familiar PLC programming environments - this makes software maintenance and standardisation much easier.
Which PLC programming environments are supported ?
MotoLogix supports the most popular IEC61131-compliant PLC programming environments, such as Siemens TIA Portal and Simotion (MotoLogix is part of the Simatic Robot Integrator program), Beckhoff TwinCAT, B&R Automation Studio, Rockwell Studio, Codesys - and of course Yaskawa MotionWorks IEC. A function block library with sample programs make it simple to adopt your own programs.
An overview and more details about all supported software environments are available on our MotoLogix Software Portal.
Another MotoLogix benefit is that the entire robot periphery, such as grippers, conveyors and sensors, can be connected and controlled directly to the cell PLC - no need to route I/Os through the robot controller to the peripheral devices - this reduces errors and significantly saves coding time. Robot status monitoring and operator interfaces can be merged with the PLC HMI visualisation device which would be there anyway.
Which Robot Models and Functionalities are supported ?
MotoLogix works with all Motoman handling robots (GP-series, MotoMini), palletizing robots of the PL-series and the MPL-series, the collaborative robots of the HC-series (!) in combination with our YRC1000, YRC1000micro and DX200 controllers. MotoLogix control supports master/slave configurations of up to 2 robots (master/slave), robot tracks, external motion axes, (synchronized) conveyor belts and vision camera systems (e.g. MotoSight2D).
Which Applications can benefit from MotoLogix PLC-based Programming ?
Typical applications for MotoLogix are:
- EOL packaging lines, for integration of Pick&Place, Pick&Pack and Palletizing robots.
- Automation around CNC and injection moulding machines, such as loading/unloading
- Quality assurance (measuring and testing, inspection)
- Collaborative robot installations, e.g. smart palletizing
- Palletizing tasks in the food and beverage industry
- Palletizing tasks in consumer goods supply chains and warehouses
The MotoLogix Software Portal
More technical information about Motologix (Overview, Installation, FAQ) is available on our MotoLogix Software Portal.
Take me to the MotoLogix Software Portal
Technical Details
- Product Type
- Interfaces
- Mobile App
- x No
- Operating System
- x No
- Min. required CPU
- x No
- Min. required RAM
- x No
- Min. required HDD Capacity
- x No
Downloads
Name | |||
Flyer Software MotoLogix Brochures | English | Brochures | English | |
Flyer Software MotoLogix Brochures | German | Brochures | German | |
Flyer MotoLogix Brochures | Spanish | Brochures | Spanish |